The Importance of Precision Machining CNC in Modern Manufacturing
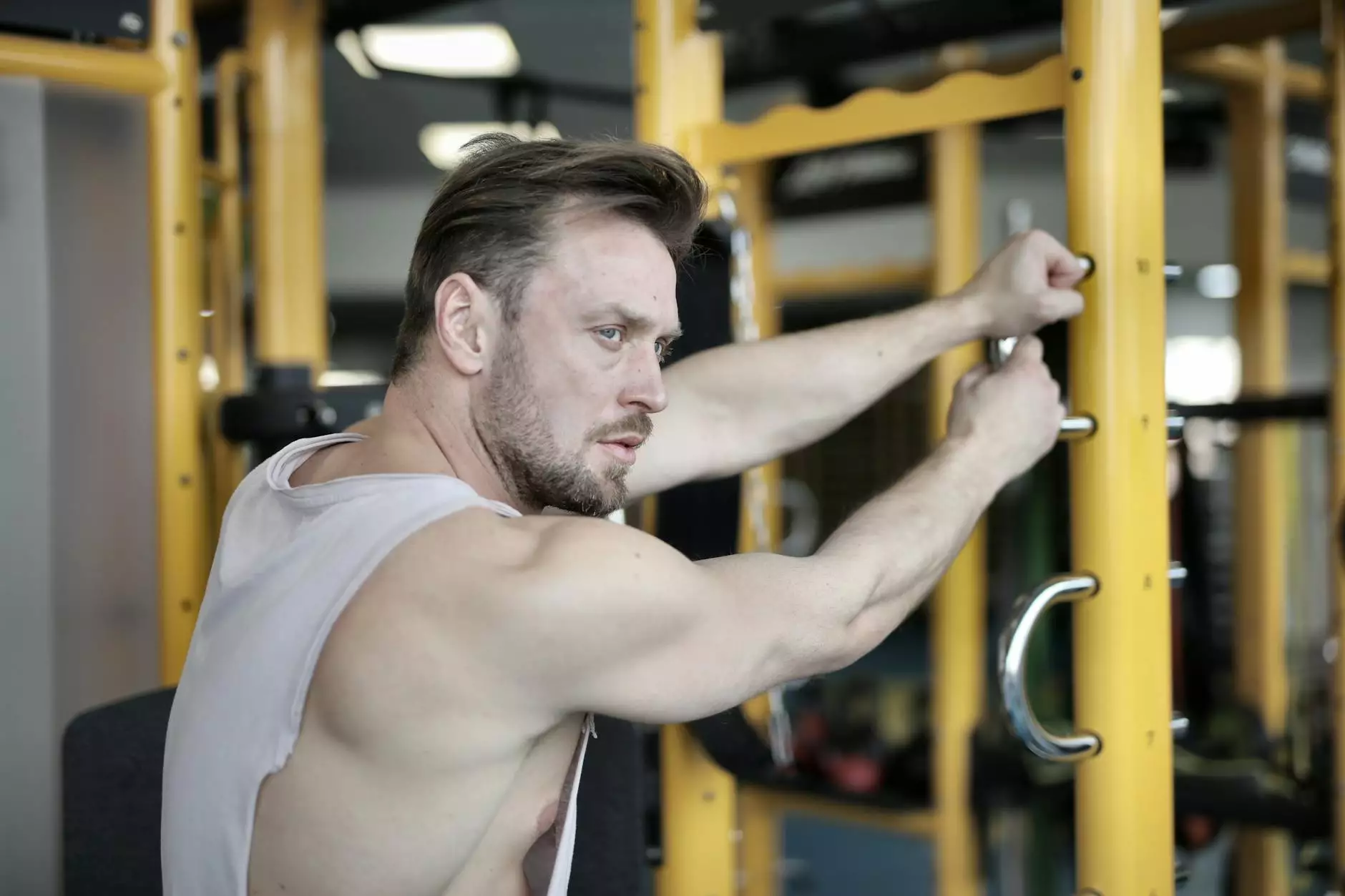
In the rapidly evolving world of manufacturing, the term precision machining CNC has emerged as a key player in enhancing productivity and ensuring quality. By integrating advanced technology with skilled craftsmanship, precision CNC machining offers a level of accuracy and efficiency that traditional methods simply cannot match. This article delves deep into the world of precision machining, exploring its significance, processes, benefits, and its transformative impact on industrial operations.
Understanding Precision Machining CNC
Computer Numerical Control (CNC) machining is a revolutionary technology that automates the control of machining tools through a computer. The term "precision machining CNC" refers to the use of CNC technology to produce high-precision components with intricate designs and tight tolerances. This section will break down the components and functionality of CNC machining.
What is CNC Machining?
- Automation: CNC machining utilizes computers for precision control of machinery, leading to automated, repeatable processes.
- Versatility: CNC machines can perform various operations, including milling, turning, drilling, and grinding.
- Accuracy: CNC machining provides unparalleled accuracy, making it ideal for complex and intricate parts required in industries such as aerospace, automotive, and medical.
How Does CNC Machining Work?
CNC machining works through a series of steps that transform raw materials into finished products:
- Design: The process begins with a computer-aided design (CAD) model that defines the specifications and geometries of the part.
- Programming: The CAD model is converted into a numerical control (NC) program using computer-aided manufacturing (CAM) software, which dictates how the CNC machine will move.
- Setup: The CNC machine is set up with the necessary tools and raw materials, ensuring everything is aligned for optimal performance.
- Machining: The machine executes the programmed instructions, cutting, shaping, and finishing the material as specified in the design.
- Inspection: Finished products are subject to quality control measures, ensuring they meet the defined specifications.
Benefits of Precision Machining CNC
The advantages of precision machining CNC are numerous and significant. This section explores the key benefits that make it indispensable in modern manufacturing.
1. Enhanced Accuracy and Precision
One of the standout features of CNC machining is its ability to produce parts with tight tolerances. This level of precision is crucial in industries where even minute discrepancies can lead to significant failures. By minimizing human error and adhering to exact specifications, CNC machining ensures that components fit perfectly and function optimally.
2. Increased Efficiency and Productivity
CNC machines are designed for high-speed operation. They can run continuously, producing parts at a rapid pace compared to manual machining processes. This continuous operation boosts productivity, enabling manufacturers to meet tight deadlines and large production volumes.
3. Cost-Effective Production
While the initial investment in CNC machines may be substantial, the long-term benefits often outweigh the costs. The efficiency and speed of CNC machining contribute to lower production costs per unit, making it a sensible choice for various manufacturing applications.
4. Flexibility and Adaptability
Modern CNC machines are equipped to handle diverse materials including metals, plastics, and composites. This flexibility allows manufacturers to adapt quickly to changing market demands and introduce new products without the need for retooling.
5. Consistent Quality
With CNC machining, every part is produced under the same conditions, leading to consistent quality across production runs. This reliability is essential for industries requiring stringent quality control and compliance with regulations.
Applications of Precision Machining CNC
The applications of precision machining CNC span a wide array of industries, each benefiting from its unique capabilities. Below are some key sectors where CNC machining plays a vital role:
Aerospace Industry
The aerospace sector demands the highest levels of precision due to safety concerns. CNC machining is used to manufacture components such as engine parts, landing gear, and structural elements with extreme accuracy, ensuring performance and reliability in aviation.
Automotive Industry
In automotive manufacturing, CNC machining produces intricate engine components, transmission systems, and body parts. Its precision improves vehicle efficiency, safety, and performance, making it an integral part of modern automotive production.
Medical Devices
The medical field requires highly specialized equipment that must meet rigorous standards. CNC machining is crucial in crafting medical devices, surgical tools, and implants, providing the necessary precision for safe and effective healthcare solutions.
Defense and Military
In defense, CNC machining is employed to manufacture specialized parts for vehicles, weaponry, and communications equipment. The accuracy and reliability of CNC-machined components are vital for operational success and safety in military applications.
The Future of Precision Machining CNC
As technology continues to advance, the field of precision machining CNC is poised for significant growth. Innovations such as additive manufacturing and smart factories are beginning to influence CNC processes, further enhancing their capabilities.
Integrating Advanced Technologies
The integration of artificial intelligence (AI) and machine learning into CNC machining is expected to optimize manufacturing efficiency. Smart CNC machines will analyze operational data for predictive maintenance, reducing downtime and improving productivity even further.
Embracing Sustainability
There is a growing emphasis on sustainable manufacturing practices. CNC machining offers the potential for reduced waste through precise cutting and material usage, contributing to environmentally responsible production techniques.
Choosing the Right CNC Machining Service
- Experience: Look for companies with a proven track record in CNC machining across various industries.
- Quality Assurance: Ensure the provider follows strict quality control measures to deliver consistent, high-quality products.
- Technology: Choose a company that utilizes the latest CNC technology for improved precision and efficiency.
- Customer Support: A responsive customer service team can help address any concerns promptly and provide support throughout the manufacturing process.
Conclusion
In conclusion, the adoption of precision machining CNC is reshaping the manufacturing landscape. Its capacity to deliver unmatched accuracy, efficiency, and cost-effectiveness is revolutionizing how products are made. As industries continue to evolve, those that embrace CNC technology will undoubtedly lead the way in innovation and quality. For businesses looking to refine their manufacturing processes, investing in precision machining CNC offers both short-term and long-term advantages that can significantly enhance operational performance and product quality.