Understanding Injection Mold Plastic: A Business Perspective
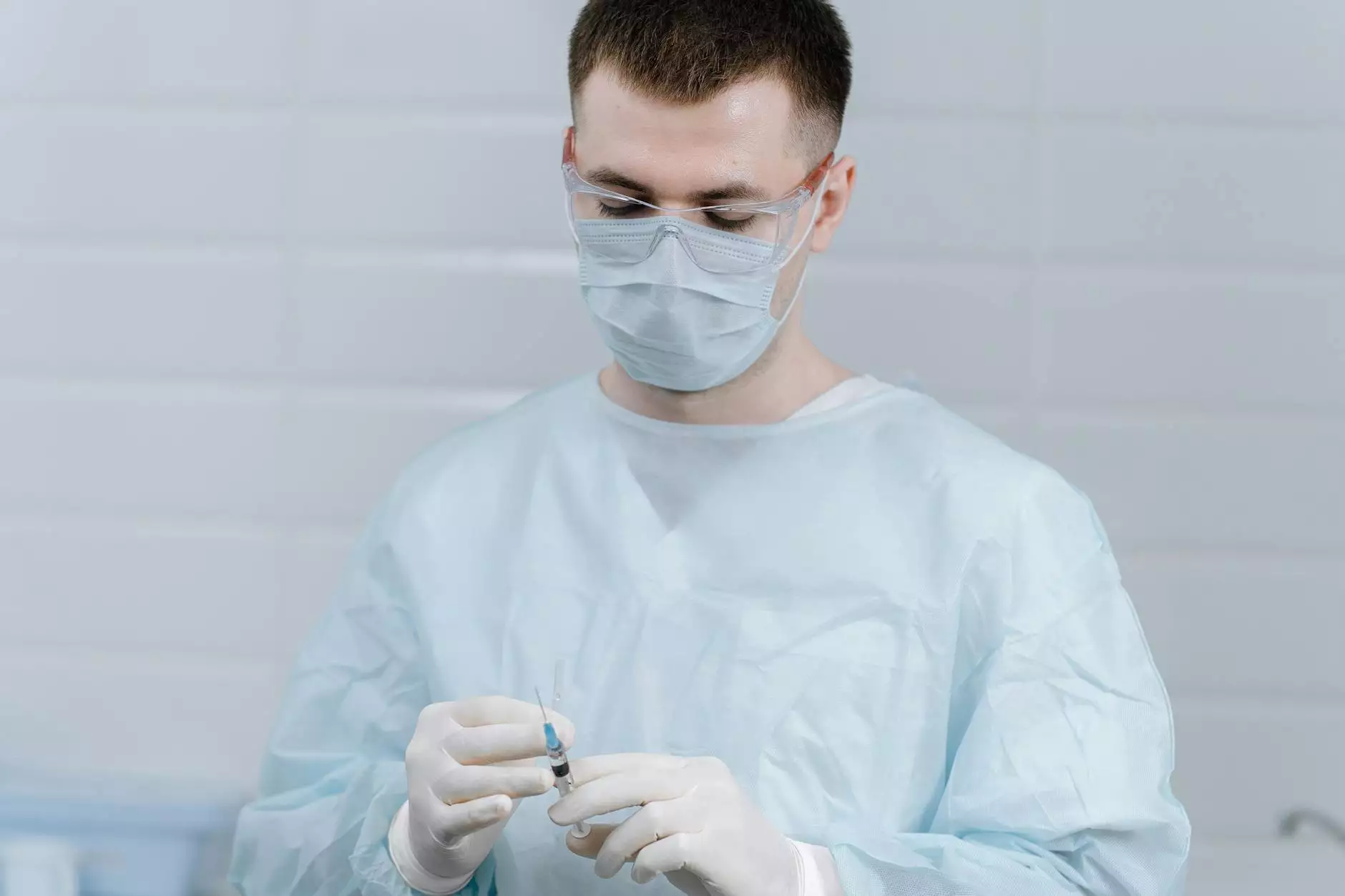
Introduction to Injection Mold Plastic
Injection mold plastic is a transformative technology widely used in the manufacturing industry. It provides a rapid and efficient way to produce parts and components across various sectors, with applications ranging from automotive to consumer electronics. This article delves deeply into the aspects of injection molding, examining its benefits, processes, and the pivotal role it plays in enhancing business productivity.
What is Injection Molding?
Injection molding is a manufacturing process that involves injecting molten material into a mold to create a desired shape and size. While it’s commonly associated with thermoplastics, it can also be used with metals and ceramics. In the case of injection mold plastic, the focus is predominantly on thermoplastics that can be reshaped upon heating.
The Process of Injection Molding
The injection molding process can be outlined in several key steps:
- Material Preparation: The plastic pellets are fed into a hopper, where they are heated until they reach a molten state.
- Injection: The molten plastic is injected into a mold cavity under high pressure, ensuring that it fills every part of the mold.
- Cooling: The plastic is allowed to cool and solidify within the mold, taking the shape of the cavity.
- Demolding: Once cooled, the mold is opened, and the solidified part is ejected.
- Finishing: Additional processes might follow, including trimming, painting, or assembling.
Advantages of Using Injection Mold Plastic
There are numerous advantages to incorporating injection mold plastic into manufacturing processes:
- High Production Efficiency: Once the initial setup is complete, the production rate is high, allowing for mass production of identical parts.
- Precision and Versatility: Injection molding can produce complex shapes with high precision. This allows for greater design flexibility in product development.
- Reduced Waste: Because the process is highly controllable, there is little surplus material, leading to reduced waste compared to traditional machining techniques.
- Cost-Effective for Large Runs: The initial costs may be high due to mold production, but the cost per unit significantly decreases with large production runs.
Applications of Injection Mold Plastic in Various Industries
Injection mold plastic is integral to diverse industries. Here are some of the main applications:
1. Automotive
In the automotive sector, injection molded parts such as dashboards, bumpers, and interior components are commonplace. The use of lightweight yet durable plastics helps improve fuel efficiency and reduce overall vehicle weight.
2. Consumer Electronics
Consumer electronics benefit significantly from this technology. Cases for smartphones, tablets, and laptops are often made via injection molding, ensuring both aesthetic appeal and functional durability.
3. Medical Devices
In healthcare, the precision of injection molded components is critical for the manufacture of devices such as syringes, inhalers, and other equipment where hygiene and reliability are paramount.
4. Household Products
Many household items, from storage containers to kitchen utensils, are produced using injection molding, allowing for cost-effective production at scale.
Choosing the Right Injection Molding Partner
For businesses looking to adopt injection molding, selecting a skilled mold fabricator is crucial. Here are some considerations:
- Experience and Expertise: Look for partners with extensive knowledge in various types of injection molds and applications.
- Technology and Equipment: A modern facility equipped with the latest injection molding technology can significantly enhance production capabilities.
- Material Compatibility: Ensure that your partner has experience with the specific plastics required for your products.
- Quality Assurance: Examine their quality control processes to ensure consistency and reliability in part production.
The Future of Injection Mold Plastic in Business
The future of injection mold plastic is bright, with innovations in materials and processes continually evolving. Here are some trends to keep an eye on:
- Biodegradable Materials: The shift towards sustainability is prompting the use of biodegradable plastics in injection molding.
- Advanced Automation: Automation in the manufacturing process is enhancing efficiency and reducing labor costs.
- 3D Printing Integration: The integration of 3D printing with injection molding can streamline product development and prototyping phases.
- Customization: The growing demand for customized solutions is leading to innovations in mold design and production techniques.
Conclusion
Injection mold plastic is a cornerstone of modern manufacturing. Its versatility, efficiency, and effectiveness make it an indispensable process in various industries. By understanding the intricacies of injection molding and leveraging its advantages, businesses can drive innovation and productivity in their operations.
As you look to the future, consider how this technology can provide a competitive edge in your manufacturing endeavors. Whether you're in automotive, consumer electronics, or medical devices, injection mold plastic will continue to shape the landscape of production and design.