Understanding Injection Molding Tools: A Comprehensive Guide
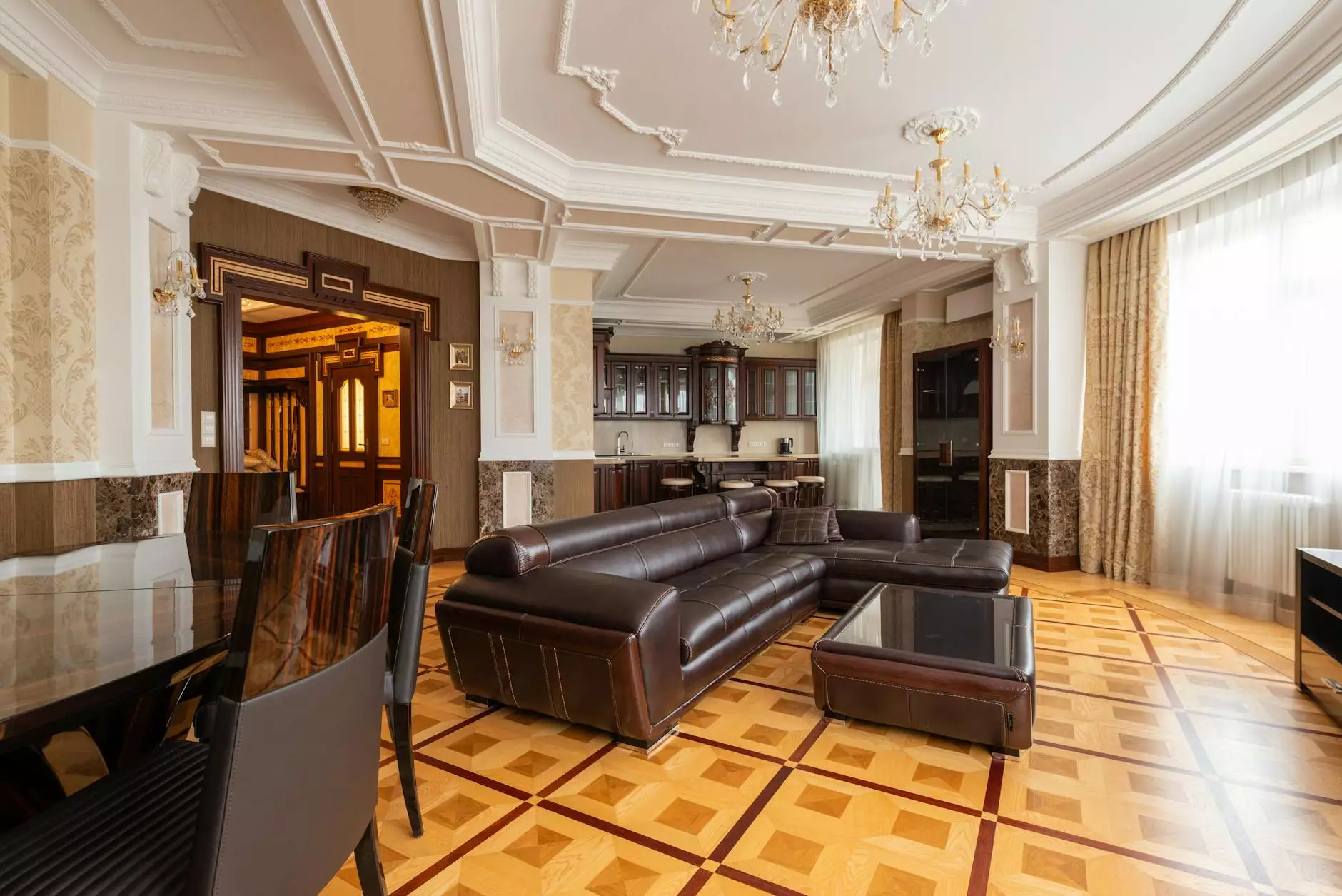
In the realm of manufacturing, the significance of tools and machinery cannot be overstated. Among these, the injection molding tool stands out as a pivotal component that aids in producing consistent, high-quality parts across various industries. This comprehensive guide delves deep into the world of injection molding tools, exploring their functionality, benefits, and the role they play in metal fabrication.
What is Injection Molding?
Injection molding is a manufacturing process used to create parts by injecting molten material into a mold. It is widely employed for producing plastic and metal components due to its efficiency and precision. When discussing injection molding tools, we are referring to the molds, machinery, and ancillary components involved in this intricate process.
The Anatomy of an Injection Molding Tool
Understanding the structure of an injection molding tool is essential for grasping how it operates. Below are the main components:
- Mold: The heart of the injection molding tool, typically made from steel or aluminum. Molds are designed to create the desired shape of the part.
- Injection Unit: This section houses the screw and barrel, where the raw material is heated and melted before being injected into the mold.
- Clamping Unit: Responsible for holding the mold in place during the injection process. It applies necessary pressure to ensure no material leaks out.
- Cooling System: After the material is injected and shaped, it needs to cool and harden. The cooling system ensures optimal temperature control.
Types of Injection Molding Tools
There are various types of injection molding tools, each tailored for specific applications:
- Single Cavity Molds: Designed to produce one part per cycle, suitable for low-volume production.
- Multi-Cavity Molds: Produces multiple parts in a single cycle, improving efficiency for larger production runs.
- Family Molds: Allows for different parts to be produced simultaneously, offering versatility.
- Stack Molds: Contains two or more cavities on multiple levels, maximizing production output.
Benefits of Injection Molding Tools
The advantages of utilizing injection molding tools in manufacturing are manifold:
- High Production Rates: Injection molding allows for rapid mass production, significantly reducing production time.
- Consistency and Precision: The automated nature of injection molding ensures each product is identical, maintaining quality standards.
- Versatility: Suitable for a variety of materials, including metals and plastics, making it adaptable for different industries.
- Cost-Effectiveness: Although the initial setup can be expensive, the long-term savings are substantial due to lower production costs and reduced waste.
Applications of Injection Molding in Metal Fabrication
Injection molding is not just limited to plastics; it plays a crucial role in metal fabrication as well. Some applications include:
- Automotive Parts: Many components in vehicles are manufactured using metal injection molding (MIM) for enhanced strength and lightweight characteristics.
- Medical Devices: MIM is utilized for creating precise and reliable components in medical applications, ensuring stringent standards are met.
- Consumer Electronics: Injection molded metal parts contribute to the sleek designs of modern electronic devices while providing durability.
Factors to Consider When Choosing Injection Molding Tools
Selecting the right injection molding tool involves a myriad of considerations to ensure optimal operation:
- Material Selection: The type of material will dictate the mold design and production process.
- Mold Design Complexity: Intricate designs may require advanced tooling and increased production time.
- Production Volume: The expected quantity of parts will influence the type of mold and materials used.
- Budget: Understanding the cost involved in mold creation and operation is crucial for financial planning.
Maintaining Your Injection Molding Tool
Proper maintenance of your injection molding tool is critical to ensuring longevity and efficiency. Here are essential maintenance tips:
- Regular Inspections: Schedule consistent checks for wear and tear, especially on crucial components like screws and barrels.
- Keep Molds Clean: Residue and contaminants can affect production quality; maintain cleanliness to ensure optimal performance.
- Lubrication: Proper lubrication of moving parts minimizes wear and improves efficiency.
- Temperature Control: Monitor the cooling systems to prevent overheating, which can lead to tool damage.
Future Trends in Injection Molding
The future of injection molding tools looks promising as technological advancements continue to shape the industry:
- 3D Printing Integration: Combining 3D printing with traditional molding techniques to create intricate designs.
- Smart Manufacturing: Incorporation of IoT technology for real-time monitoring and enhanced efficiency.
- Sustainability: The development of biodegradable materials for environmentally friendly injection molding practices.
Conclusion
In conclusion, understanding the intricacies of injection molding tools is essential for anyone involved in metal fabrication or manufacturing. The ability to produce high-quality, consistent parts rapidly makes injection molding a go-to process across various industries. By investing in the right tools and following best practices, businesses can optimize their production processes, ensuring they stay competitive in the ever-evolving market landscape.
For more information about quality injection molding tools and services, visit Deepmould.net today!