Comprehensive Guide to Silicone Membrane for Vacuum Forming: Enhance Your Business Efficiency
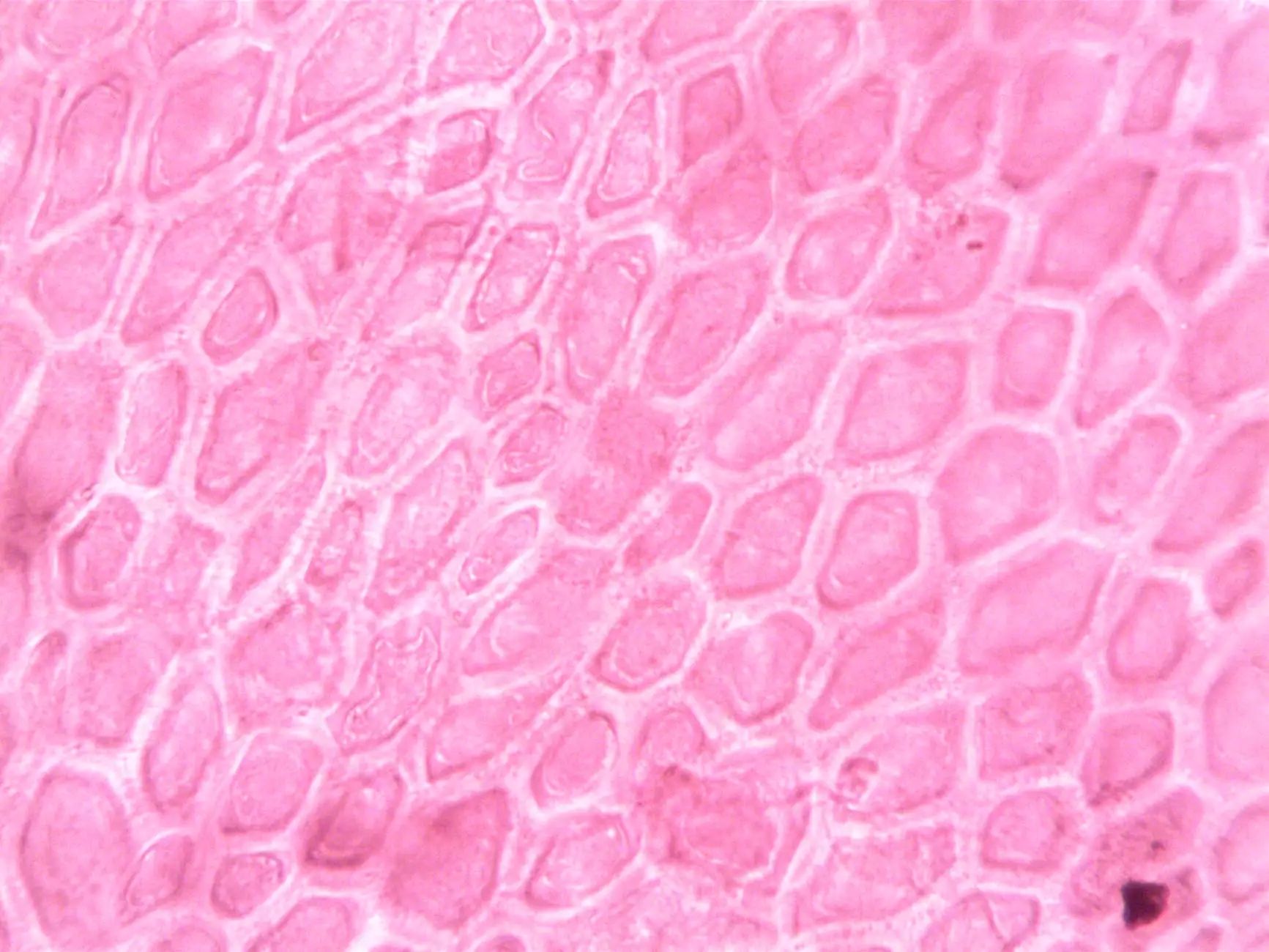
In the competitive world of manufacturing and fabrication, having the right tools and materials is crucial for achieving excellence and staying ahead of the curve. One of the essential components in modern vacuum forming processes is the silicone membrane for vacuum forming. This specialized membrane plays a vital role in ensuring precision, durability, and high-quality output, making it a key investment for businesses looking to improve their production capabilities.
Understanding Vacuum Forming and Its Importance in Modern Manufacturing
Vacuum forming is a popular manufacturing process used primarily in packaging, prototyping, automotive parts, electronics, and consumer products. It involves heating a plastic sheet until pliable, then stretching it over a mold, and applying vacuum pressure to form the material seamlessly against the mold surface. This technique offers several advantages, including reduced production costs, rapid tooling, and the ability to produce complex shapes with high precision.
However, the success of vacuum forming relies heavily on the quality of the vacuum system parts, especially the membranes that create the necessary seal and pressure distribution. This is where silicone membrane for vacuum forming becomes indispensable.
The Critical Role of Silicone Membranes in Vacuum Forming
What Is a Silicone Membrane?
A silicone membrane is a flexible, heat-resistant sheet primarily made from high-grade silicone rubber. It serves as a critical component in vacuum forming machines, acting as a durable, customizable barrier between the heater and the mold. Its flexibility allows it to conform to complex shapes, while its heat resistance ensures it can operate consistently at high temperatures without degradation.
Why Use Silicone Membranes for Vacuum Forming?
- Superior Heat Resistance: Silicone membranes can withstand extreme temperatures, often exceeding 300°C (572°F), making them ideal for continuous operation in high-temperature environments.
- Exceptional Flexibility and Conformability: They can adapt to intricate mold details, ensuring precise replication of complex designs.
- Durability and Longevity: High-quality silicone membranes resist tearing, cracking, and chemical degradation, reducing maintenance costs and downtime.
- Ease of Maintenance: Silicone membranes are easy to clean and maintain, supporting consistent production quality.
- Chemical Resistance: They resist oils, greases, and other chemicals, maintaining their integrity over time.
Types of Membranes in Vacuum Forming Systems
While silicone membranes are among the most popular, there are other types of membranes used in vacuum forming, each with specific advantages:
- Rubber Membranes: Including natural rubber and synthetic variants, these provide excellent elasticity and sealing capabilities but may have limited heat resistance.
- Natural Rubber Membranes: Known for their high elasticity and cost-effectiveness but less suited for high-temperature applications.
- Rubber Membranes: Often used in applications requiring tight seals and flexibility.
Choosing the right membrane depends on your specific production needs, materials, and temperature requirements.
Advantages of Using Silicone Membrane for Vacuum Forming
Enhanced Precision and Consistency
Silicone membranes enable a uniform vacuum seal, resulting in highly accurate and consistent product shapes. This precision is critical for applications in aerospace, automotive, and medical device manufacturing, where tolerances are stringent.
Improved Durability and Cost-Effectiveness
Due to their exceptional mechanical and thermal properties, silicone membranes typically outlast other materials, providing a better return on investment. Their resistance to wear and chemical attack reduces replacement frequency and downtime.
Versatility Across Applications
The adaptability of silicone membranes allows them to be used across diverse industries, from small-scale prototype production to large-volume manufacturing. They can also be custom-sized and shaped to fit specific machinery and mold configurations.
Energy Efficiency and Process Optimization
By providing a consistent vacuum seal with minimal energy loss, silicone membranes contribute to more efficient energy utilization in the manufacturing process, reducing operational costs over time.
Choosing the Right Silicone Membrane Supplier
Key Factors to Consider
- Quality and Certifications: Ensure the supplier adheres to international quality standards such as ISO 9001, guaranteeing reliable product quality.
- Customization Options: Ability to tailor membrane dimensions, thickness, and surface finish to match your exact requirements.
- Material Selection: Availability of different silicone formulations for high-temperature, chemical resistance, or specific flexibility needs.
- Technical Support and Service: Access to expert guidance for installation, maintenance, and troubleshooting.
- Cost and Delivery Times: Competitive pricing combined with timely delivery to keep your production on schedule.
Why Buy Membranes from Profound Suppliers Like vacuum-presses.com
vacuum-presses.com is a leading provider specializing in buy membranes for vacuum forming systems, offering a comprehensive range of silicone membranes, rubber membranes, and natural rubber membranes. Their expertise ensures that clients receive high-quality, durable, and precisely fabricated membranes that elevate their manufacturing processes.
Partnering with trusted suppliers like vacuum-presses.com guarantees access to the latest membrane technologies, professional support, and custom solutions designed to optimize your vacuum system and manufacturing efficiency.
Application Fields for Silicone Membrane for Vacuum Forming
- Packaging Industry: For creating customized enclosures, containers, and protective packaging with high precision.
- Prototyping and R&D: In product development, silicone membranes enable rapid testing and iteration of new designs.
- Automotive Parts Manufacturing: Forming complex interior and exterior components with exacting standards.
- Medical Devices: Ensuring clean, precise forming of sensitive products used in healthcare.
- Electronics: Manufacturing highly detailed housings and components requiring intricate molding.
Maintenance and Care of Silicone Membranes
To maximize the lifespan and performance of your silicone membranes, consistent maintenance is essential. Implement the following best practices:
- Regular Cleaning: Use mild detergents and non-abrasive tools to remove dust, oil, and residue.
- Periodic Inspection: Check for signs of wear, tears, or chemical damage, and replace membranes when necessary.
- Proper Storage: Store membranes in a clean, dry environment away from direct sunlight and extreme temperatures.
- Use Compatible Materials: Ensure that the forming materials and chemicals used are compatible with silicone to prevent degradation.
Conclusion: Elevate Your Manufacturing with High-Quality Silicone Membranes
Investing in a silicone membrane for vacuum forming is a strategic decision that can significantly improve your manufacturing efficiency, product quality, and operational longevity. With their outstanding heat resistance, flexibility, and durability, silicone membranes stand out as the best choice for demanding vacuum forming applications across numerous industries.
Partnering with reliable suppliers like vacuum-presses.com ensures you acquire premium membranes tailored to your needs, supported by expert service and ongoing innovation. Embrace the advantages of advanced membrane technology and unlock new levels of production excellence today.